Tips To Solve Problem CNC Waterjet Troubleshooting.
Solve The Problem Of CNC Waterjet Troubleshooting:
1) Over stroking: (waterjet troubleshooting)
During startup, it is common for intensifiers to peak and change between pressures. But during normal operation, it should work smoothly to the left-right way at the same speed. However, if the hydraulic piston travels faster too much in one or both directions than the pump can support and an alarm will be heard.
If over stroking is happened, your first step is to reset the alarm and then:
>Cutting heads turn off
>The pump turns on and gives time to build up pressure
>Cutting heads turn on
>Intensifier stroke rate monitor either manually or by operator surface indicator.
2) Short Seal Life: (waterjet troubleshooting)
While seals live naturally short. Some actions you can follow to help them to extend the last longer interval are:
>Make sure to use the right water quality within an acceptable range.
>During seal replacement, clean all parts thoroughly to eliminate debris.
>Ensuring no cracks, check all parts of the high-pressure cylinder.
>Verifying the water volume and pressure meet the minimum required standard.
>Make sure the plunger bearing is not worn.
3) Water leaks: (waterjet troubleshooting)
Another troubleshooting area is water leakage. The most common cause of water leaks is high-pressure hoops and seals damaging the intensifier. However, you want to focus on how leaks are happening and where they are coming from.
>If you observe a drop of water in every few strokes, it means that seals’ lives are nearing the endpoint and have to be replaced within a reasonable time period.
>If warm water leaks on the adapter from the weep hole, it means the high-pressure water tubing fitting is not tight enough and their end is damaged or the adapter has failed.
>If you notice the warm water leaking on the check valve from the weep hole, it means that the output adapter is loose and fails the high-pressure poppet seat or the check valve is damaged.
>If cold water leaks from the end bell that means the check valve O-ring has failed and it needs to be replaced.
>Hot or warm water coming from the end cap which indicates the static end cylinder high-pressure seal has failed and needs to replace.
>If cylinder dynamic end water leakage happens that means the high-pressure seals on their end have failed.
4) Hydraulic fluid pressure failure troubleshooting:
5) Low water pressure: (waterjet troubleshooting)
If you notice low water pressure when the cutting head-on when water travels from the intensifier away. You should take these steps.
>To make sure the orifice is in good working order is not defective or damaged. If it does not work well, replace it.
>Verify the leaking is happening or not by checking the on/off valve. If leaking happens, repair it.
>Check valves, if necessary repair or replace it after the examination.
Double-check the intensifier, not a stroke, when the cutting water jet head is turned off. If stroke, check the high-pressure tubing leaks and bleed down valve and replace or repair it. If no leaks and problems are created by poppets of high pressure and low pressure then replace or repair the poppets.
If the water jet system senses low pressure of water traveling to the in-testifier. The system will be protected by the shut pump off without running an intensifier with enough pressure.
If this happens, do the following steps:
>Make sure that the water comes to the pump.
>Water filters swap out
>Make sure inlet-cutting water valves have not clogged or failed
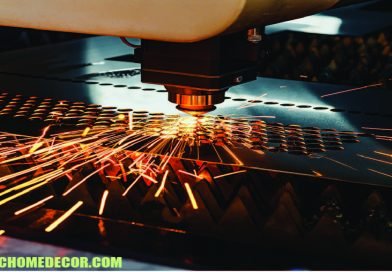
What About CNC Laser Cutter Engraver Machine:
CNC Laser Cutter Engraver Machine: Invention of new things has arrived at a point where regular people can buy a