The CNC Laser Cutting Machine and Procedure:
CNC Laser Cutting Machine and Procedure:
Laser cutting is a non-contact, warm based creation process appropriate for metal and non-metal materials. For the laser cutting procedure to run easily and at ideal limit, a few variables ought to be thought about, for example, the laser cutting machine’s setup and settings, the material being cut and its properties, and the sort of laser and help gas utilized.
1. Laser Cutting Machine Components and Mechanics:
Rather than mechanical cutting, which uses cutting apparatuses and force driven gear, and waterjet cutting, which uses pressurized water and rough material, laser cutting utilizes a laser-cutting machine to create cuts, inscriptions, and markings. While laser slicing machines shift from model to demonstrate and application to application, the run of the mill arrangement incorporates a laser resonator get together, mirrors, and a laser cutting head which contains a laser centering focal point, a pressurized gas get together, and a spout.
The essential laser cutting procedure incorporates the accompanying stages:
- Bar age
- Bar centering
- Limited warming and softening
- Material discharge
- Bar development
2. Laser Cutting Machine’s Shaft Generation:
The expression “laser” originates from the abbreviation LASER or Light Amplification by Stimulated Emission of Radiation. This abbreviation sums up the essential standards of laser age—incitement and enhancement. Alongside these standards, the laser resonator utilizes the procedures of unconstrained emanation, invigorated discharge to deliver a high-power light emission that is both spatially, and frightfully lucid (i.e., a laser bar).
i. Unconstrained emanation:
The laser resonator contains a functioning laser medium (e.g., CO2, Nd:YAG, and so on.), the electrons of which are invigorated by an outside vitality source, for example, a glimmer light or electrical circular segment. As the medium gets and assimilates vitality, its particles experience a procedure known as unconstrained discharge. During this procedure, vitality consumed by a molecule makes the particle’s electrons quickly hop to a higher vitality level and afterward come back to their ground state. Upon the electrons’ arrival to their ground express, the particle produces a photon of light.
ii. Animated Emission:
The photons that are delivered by unconstrained outflow travel inside the medium, which is contained in a depression of the laser resonator between two mirrors. One mirror is intelligent to keep photons going inside the medium, so they keep on spreading invigorated emanations, and the other mirror is halfway trans missive to permit a few photons to get away. Invigorated outflow is the procedure where a photon (i.e., the episode photon) animates a particle that is as of now at a higher vitality level.
This association powers the invigorated iota to drop to its ground state by transmitting a second photon of the equivalent fixed frequency or reasonable with the occurrence photon. The procedure of one photon engendering the outflow of another photon enhances the quality and force of the light shaft.
Along these lines, the invigorated emanation of light photons (i.e., a kind of electromagnetic radiation) causes the intensification of light; as it were, light enhancement by the animated discharge of radiation. Inappropriately adjusted photons inside the resonator go through the in part transmissive mirror without being reflected into the medium, creating the underlying laser shaft. Once produced, the pillar enters the laser cutting head and is coordinated by mirrors into the centering focal point.
3. Laser Cutting Machine’s Pillar Focusing:
The centering focal point centers the laser pillar through the focal point of the spout toward the finish of the laser slicing head episode to the work piece’s surface. By centering the shaft, the focal point focuses the bar’s vitality into a littler spot, which expands the bar’s force (I). The accompanying condition represents the hidden standard behind this event:
4. Laser cutting machine definition - how does a laser shaper work?
Where P speaks to the intensity of the underlying laser pillar, and πr2 speaks to the cross-sectional territory of the shaft. As the focal point centers the laser pillar, the sweep (r) of the bar diminishes; this decline in range lessens the cross-sectional zone of the bar, which thusly expands its force since its capacity is presently disseminated over a little territory.
5. Laser Cutting Machine’s Limited Heating and Melting, and Material Ejection:
As the bar strikes the material’s surface, the material assimilates the radiation, expanding the inner vitality and creating heat. The high power of the laser bar permits it to warmth, dissolve, and incompletely or totally disintegrate a confined territory of the work piece’s surface. The debilitating and expulsion of the influenced territory of the material structures the ideal cuts.
Guided into the laser slicing head and streaming coaxially to the engaged pillar, the help gas—likewise alluded to as the cutting gas—is utilized to secure and cool the centering focal point, and might be utilized to oust liquefied material out of the kerf—the width of the material evacuated and of the cut created—and bolster the cutting procedure. Laser cutting utilizes a few distinct sorts of material cutting and evacuation components, including combination cutting, compound corruption cutting, vanishing cutting, scribing, and oxidation cutting.
i. Combination Cutting:
Also alluded to as dormant gas liquefies shearing or latent gas cutting, combination cutting is utilized by CO2 and Nd: YAG laser cutting machines. The laser bar created by the cutting machine softens the workpiece, and the dissolved material is ousted through the base of the kerf by a stream of the help gas utilized. The help gas and the help gas pressure utilized are reliant on the sort of material being cut, however, the latent gas is constantly picked dependent on its absence of substance reactivity concerning the material. This system is reasonable for laser cutting most metals and thermoplastics.
ii. Concoction Degradation:
Chemical corruption is utilized by CO2 laser cutting machines and is reasonable for laser cutting thermoset polymers and natural material, for example, wood. As thermoset and natural materials don’t liquefy when warmth is applied, the laser shaft consumes the material rather, diminishing it to carbon and smoke.
iii. Vanishing Cutting:
Evaporation cutting is utilized by CO2 laser cutting machines and is appropriate for materials, for example, laser slicing acrylic and polyacetal because of the closeness of their liquefying and breaking points. Since the laser dissipates material vanishes along with the cut, the edge delivered is commonly gleaming and clean.
iv. Scribing:
Scribing is utilized by CO2 and Nd: YAG laser slicing machines to create halfway or completely infiltrating sections or punctures, for the most part on earthenware production or silicon chips. These scores and punctures take into consideration mechanical breaking along the debilitated basic lines.
v. Oxidation Cutting:
Also alluded to as fire oxygen cutting, oxidation cutting is utilized by CO2 and Nd: YAG laser cutting machines and is appropriate for laser cutting of gentle and carbon steel. Oxidation cutting is one case of the receptive gas soften shearing cutting component, which explicitly utilizes synthetically responsive help gases. Similarly, as with inactivity, the reactivity of a help gas is comparative with the material being cut.
Oxidation cutting, as the name infers, utilizes oxygen as the help gas, which exothermically responds with the material. The warmth created quickens the cutting procedure and produces an oxidized softened edge which can be effectively expelled by a gas stream to consider a cleaner, laser-cut edge.
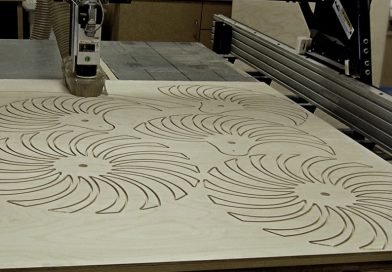
CNC Wood Router: Take The Next level To The Wood Working.
CNC Wood Router For Wood Working: CNC wood working router is a machine that naturally cuts the wood in an
6. Laser Cutting Machine’s Shaft Movement:
When the confined warming, softening or disintegrating has begun, the machine moves the territory of material evacuation over the workpiece to create the full cut. The machine accomplishes the development either by changing the intelligent mirrors, controlling the laser cutting head, or controlling the workpiece.There are three distinct designs for laser cutting machines, characterized by the manner by which the laser pillar moves or is moved over the material: moving material, flying optics, and a half and half laser cutting frameworks.
i. Moving Material:
Moving material laser cutting machines include a fixed laser pillar and a mobile slicing surface to which the material is joined. The work pieces precisely moved around the fixed shaft to deliver the essential cuts. This setup takes into consideration a uniform and predictable stalemate separation and requires fewer optical parts.
ii. Flying Optics:
Flying optics laser cutting machines highlight a portable laser shaper head and a fixed work piece. The cutting head moves the shaft over the fixed work piece in the X-and Y-tomahawks to create the fundamental cuts. The adaptability of flying optics machines is reasonable for cutting materials with variable thickness and sizes, just as taking into account quicker handling occasions.
Nevertheless, since the bar is constantly moving, the changing bar length must be thought about all through the procedure. The changing shaft length can be constrained by collimation (arrangement of the optics), utilizing a steady bar length hub, or utilizing a versatile optics or capacitive tallness control framework fit for making the essential changes continuously.
iii. Half breed:
Hybrid laser cutting machines offer a blend of the traits found on moving material and flying optics machines. These machines highlight a material taking care of table that proceeds onward one pivot (ordinarily the X-hub) and a laser head that proceeds onward another (typically the Y-hub). Half-and-half frameworks take into consideration more reliable pillar conveyance, and diminished force misfortune and more prominent limit per watt contrasted with flying optics frameworks.
Lasers are delivered as either beat shafts or nonstop wave bars. Beat bars are delivered as short explosions of intensity yield.